
Investment Casting
INVESTMENT CASTING IN INDUSTRIAL COMPONENTS
HIGH GRADE STEEL COMPONENTS BY USING INVESTMENT CASTING
VSC is one of the largest steel-casting companies in the world and produces complex castings with extreme precision using the “lost-wax” method. Thanks to this versatile method our engineers have considerable freedom in the product design and choice of materials. This means that in consultation with you we can produce optimum castings that meet your exact wishes and requirements.

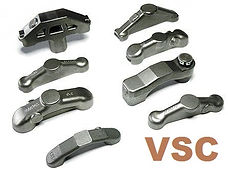
VALVE BRIDGE
-
Fuel savings due to lower product weight and inertia
-
Suitable for mass production without post processing
-
Casting in hardened steel with an extremely smooth surface
-
Lower costs from cutting out the need for hardening and mechanical post-processing
PROCESS
VSC Engineering optimises the design for mass production without post-processing. Solid design, optimum functionality at the lowest possible production cost. An oil channel can also be cast at the same time in the chamber where the valve stem fits (pocket). Lower weight through ‘Near Net Shape’ design. This results in decreased inertia of the valve mechanism, saving fuel. Component cast in hardened steel without extra post-processing, providing considerable cost savings.
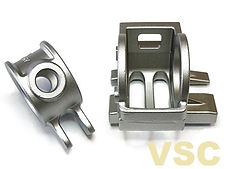
SHIFTING MECHANISM
Steel switching mechanism for a manual transmission. With this mechanism, movements of the shifting fingers are transferred to the transmission according to the shifting pattern.
ADVANTAGES
-
No machining required
-
Smooth, wear-resistant surface
-
Component is delivered ‘ready for use’
-
High-quality surface guarantees smooth shifting
PROCESS
‘Near Net Shape’ (NNS) design is avoid need for machining. After calibration this part is case-hardened for the hard surface with retention of the tough inner part. The design freedom of the casting process makes the shifting arm string. Ribs are added to the design only at places where this is necessary to maintain strength.

APPLICATION
Valve in the exhaust of an engine with a turbo. This valve bridges the turbo and keeps it from building up excessive pressure if the engine is at high revs or is loaded more heavily.
ADVANTAGES
-
Heat-resistant and wear-resistant steel alloy
-
Minimal post-processing required
-
Big savings in material costs
PROCESS
-
Inconel alloys are extremely durable and heat-resistant. This makes the material suitable for applications in turbochargers with exhaust gasses reaching 800° C. Since Inconel alloys are difficult to process, as many precise tolerances as possible are cast beforehand. Very few or no mechanical post-processing steps are needed.